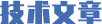
2025年04月18日 11:29昆山汉吉龙测控技术有限公司点击量:22
机械故障诊断技术的发展历程
“诊断”一词涵盖了众多领域,既包括医疗领域中的人体诊断,也包括环境监测诊断技术。在工程领域,特别是机械设备、电子仪器、工程结构以及计算机系统的诊断技术。尽管机械故障诊断技术起步相对较晚,但自六十年代中期尤其是七十年代以来,其发展速度迅猛。这得益于多个方面的推动,包括技术进步、市场需求以及工业应用的不断拓展。
一、机械故障诊断技术的飞速发展得益于前沿学科的推动
近年来,国际机械故障诊断技术取得了显著进展,这主要归功于两大因素:一是经济效益的驱动,二是前沿学科技术的支撑。从故障诊断的演变历程来看,这些前沿学科技术发挥着至关重要的作用。过去十几年里,该领域经历了以下几个重要的转变:首先,传统技术的束缚被打破,技术之间相互渗透融合;其次,前沿技术的学术思想活跃,为技术创新提供了源源不断的动力;最后,通过促进旧学科和基础学科的更新,产生了许多新的学科分支。
二、机械故障诊断技术的实用价值在于其确诊能力
机械故障诊断的存在与发展,与其在实际应用中的确诊能力密不可分。为了确保准确诊断,必须满足一系列标准,包括准确估计机器内部故障的位置与类型,区分主导与伴随故障,判断主导故障的发生与转移,以及对潜在故障的长期发展趋势做出预测。同时,多种因素会影响故障的确诊能力,如设备结构的复杂性、可维护性,潜在故障的多样性,故障信息的完备性,诊断信息的准确性,以及专家经验的积累等。
三、当前诊断技术的几个研究热点
(1)增强对常见与多发机械故障的诊断能力;
(2)探索信息融合与特征提取的新方法;
(3)构建数据挖掘与数据仓库,以充分利用诊断数据;
(4)发展智能诊断技术,提高诊断的自动化水平;
(5)实现远程诊断,方便快捷地解决机械故障问题。
1.2 机械故障诊断的目的与核心内容
首先,我们来探讨机械故障的定义与分类。机械故障,简而言之,就是指机械设备在运行过程中出现的异常状况,这些状况可能影响设备的正常功能,甚至导致设备停机。为了更有效地进行故障诊断,我们通常将这些故障进行分类,以便针对不同类型的故障采取相应的诊断措施。
故障的定义
设备在运行过程中,会呈现出不同的状态。其中,故障状态、异常状态和正常状态是设备的基本状态分类。当设备的功能指标低于其正常时的低限度,即设备无法完成其规定的功能时,这种情况就被称为故障。
2. 故障的分类
机械设备的故障可以依据不同的标准进行分类。按故障的性质,我们可以将其分为器质性故障和操作型故障。器质性故障源于机器本身,如转子弯曲或叶片断裂,这类故障往往具有偶然性和突发性,需立即停机检查并修复。而操作型故障则多由操作人员误操作或工艺参数选用不当导致。
此外,按故障发生的进程,故障可分为突发型和渐发型。突发型故障无预兆,破坏性大,因此需对关键设备的重要部位进行连续监测。渐发型故障则因设备零件技术指标逐渐恶化而引发,是机械设备修理中的常见类型,约占50~80%。其特点包括:故障多出现在零件有效寿命的后期,即耗损故障期;具有规律性,可预防;且故障发生频率与机器运行时间相关。
同时,按发生故障的时间,HOJOLO将故障分为磨合期故障、正常使用期故障和耗损期故障。而按故障的复杂程度,则可分为单一型故障和复合型故障。最后,按故障的后果严重程度,可分为轻微故障、一般故障、严重故障和致命故障。
3. 故障的规律
(1)故障率
故障率是衡量设备性能的重要指标。它表示某种设备在特定时间段内发生故障的概率。具体来说,设备的故障率是指在单位时间内,发生故障的设备台数与同时期内仍在工作的设备台数的百分比。这种瞬时故障率具有统计特性,能够帮助我们了解设备的可靠性和耐久性。
(2)典型故障曲线——“浴盆”曲线
大多数设备的故障率随时间变化,呈现出一种特定的曲线形状,这种曲线被称为“浴盆曲线”。该曲线的特点是两头高、中间低,分为三个明显的阶段:早期故障期、偶然故障期和严重(耗损)故障期。通过分析这种典型故障曲线,我们可以更好地了解设备故障的规律和特点,从而采取有效的预防和维修措施。
早期故障期:
新设备在初始工作期,由于新元件之间的磨合不足或装配问题,加上设计、选材及加工质量的差异,往往会出现故障率较高的现象。但随着运行时间的推移,故障率会迅速降低。
偶然故障期(寿命期):
当设备进入正常运行阶段,其故障率保持在一个较低且相对稳定的水平。此阶段的故障具有随机性,与设备的新旧程度无关,因此难以预测,且无法通过简单的磨合来消除。
严重(耗损)故障期:
随着设备使用进入后期,由于长期磨损、疲劳和腐蚀等因素的影响,故障率会逐渐上升。这一阶段的设备需要更加密切的关注和维修。
值得注意的是,这三个故障期是对大多数设备而言的普遍规律,但并非所有设备都会经历这三个阶段,有些设备可能只会表现出其中的一个或两个阶段。
二、机械故障诊断技术的实质与内涵
机械故障诊断技术,简而言之,就是为机器“看病”的技术。它旨在了解和掌握机器在运行过程中的状态,判断其整体或局部是否正常,及时发现并确定故障原因,同时预测故障的发展趋势。该技术涵盖了“监测”与“诊断”两大核心环节。
在实际应用中,故障诊断技术需紧密结合工程实际,致力于解决机器在设计、制造及运行过程中遇到的问题。此外,高可靠性、注重经济效益以及多学科交叉融合的特点,使得故障诊断成为一项综合性的技术。
值得注意的是,故障诊断不仅是一种从整体到零部件的反求技术,更是一个复杂的系统工程。在诊断过程中,核心问题在于模式识别,即对症状和故障的识别、分类和聚类。为了确保诊断的准确性,需要充分收集并正确处理相关信息,实现有效融合。同时,机器故障的传递具有整体性与层级性,这为故障诊断带来了新的挑战。
在整体性方面,机器的故障症状往往表现为机器整体的症状,而非单一零件的症状。这要求诊断人员具备全局观念,从整体角度分析故障原因。而在层级性方面,故障的影响范围具有一定的层次性。当机器内部出现故障时,其症状不仅会反映在故障本身,还会影响到相关组件和部件。因此,在诊断过程中,需要仔细分析故障信息的传递路径和层次关系,以准确判断故障位置和原因。
与机器的层级系统紧密相关的是近似可分系统。
三、机械状态监测与故障诊断的核心理念
核心理念在于确保机器能够稳定、高效地发挥其预设功能。这涵盖了准确识别机器的运行状态及故障类型,从而保障其安全且持续地运行,实现效益化。同时,一旦机器出现异常或故障,能够迅速且精确地进行诊断,以便采取适当的预知性维修措施,缩短维修时间,提升维修质量,并降低维修成本。此外,通过性能评估所收集的数据与信息,还可为机器的优化设计与制造提供有力的支持。
四、机械状态监测与故障诊断的涵盖内容
机械状态监测与故障诊断的核心内容主要涵盖两个方面:其一是对机器的运行状态进行持续监测,其二是在发现异常或故障时进行深入的诊断。通过这些手段,我们可以及时掌握机器的工作状况,预测并防范潜在的风险,确保机器的稳定、高效运行。
状态监测
通过运用多种测量、分析和判别技术,我们能够深入了解机器当前的运行状态。结合机器的历史运行数据和现有条件,这一过程为机器的性能评估、合理使用、安全运作以及故障诊断提供了坚实的基础。
2. 故障诊断
在深入了解机器当前运行状态的基础上,我们需要进一步探究故障的具体性质、程度、所在部位、成因以及未来发展趋势。这一过程旨在为故障的预报、控制、调整以及维护提供科学依据。它涵盖了以下四个关键环节:
信号检测:选用合适的传感器,捕捉与机器状态紧密相关的动态信号。
特征提取:运用信号处理技术,从动态信号中筛选出与机器状态及故障特征紧密相关的信息。
状态识别:依据提取的特征,通过建立判别函数、设定判别标准以及进行比较等步骤,来准确识别机器的状态及故障。
诊断决策:综合分析机器的当前状态、故障类型、部位、性质及发展趋势,从而做出相应的决策,如继续监测、加强重点监测或安排停机维修等。
1.3 诊断信息的来源与获取
信息,作为判别和识别的关键资料,在故障诊断中扮演着至关重要的角色。而信号,作为系统的输入与输出,常以电信号的形式出现,携带信息的电压或电流即被定义为信号。为了获取这些诊断信息,我们采取了多种方法:
整机性能测定:通过测量设备的输出与输入关系,来全面了解设备的运行状态。
零部件性能测定:专注于那些对设备可靠性至关重要的关键零部件,为诊断提供深入的信息。
直接观察法:凭借经验,通过视觉、触觉和听觉来初步判断机器的状态。这种方法虽简单,但适用于能直接观察到的机器零件。同时,借助滚动轴承检测仪、工业内窥镜等工具,可以进一步扩大观察范围。
动态信息检测法:利用传感器技术,捕捉机器运行过程中的动态信息,如振动、噪声、温度等。这些信息从不同角度反映了机器的状态和故障特点。其中,振动信号检测法和噪声信号检测法是常用的方法,通过分析振动和噪声的强度及动态信号,可以更准确地判断机器的故障部位和程度。
磨损残留物测定:机器在运行过程中因摩擦产生的磨损残留物,通过润滑油取样和分析,可以判断磨损的部位及严重程度。
综上所述,诊断信息的来源与获取是故障诊断的基础,通过多种方法的综合运用,我们可以更全面、准确地了解机器的运行状态和故障情况。
1.4 机械故障诊断方法的分类
机械故障诊断的方法可以依据不同的视角进行归类。其中,一种常见的分类方式是按照诊断的目的与要求来划分。
1.4.1 功能诊断与运行诊断
功能诊断主要针对新安装或刚经过维修的设备,旨在检验其运行时的各项功能是否正常。通过此诊断,可以及时发现并调整机器的不正常状态,确保其能正常投入使用。而运行诊断则是对正在运行的机器进行持续监测,旨在发现并跟踪故障的发生与发展过程,为故障的及时处理提供依据。
2. 直接诊断与间接诊断
直接诊断,即直接对关键零部件的状态进行检测,例如测量主轴承的间隙、观察齿面的磨损情况、检查叶片是否断裂,以及测量管道壁厚等。而当由于机器的结构或工作条件的限制,无法直接进行诊断时,我们可以采用间接诊断方法。这种方法主要是通过收集二次信息,来对机器中关键零部件的状态进行推断和判断。
3. 定期诊断与连续监控
在机器维护中,我们经常面临两种不同的诊断方式:定期诊断与连续监控。这两种方式的选择,取决于关键设备的性能下降速度、故障的可预测性,以及故障对生产的影响程度。对于性能下降缓慢、故障可预测的设备,我们可以采用定期诊断的方式;而对于性能下降迅速、故障不可预测或影响严重的设备,则更适合采用连续监控的策略。
在线诊断与离线诊断
在线诊断,类似于连续监控,需要配备一套完整的信号采集、处理和识别的监测诊断系统,实时监测机器的状态。而离线诊断,则是通过某种手段记录现场机器运行的动态信号,然后将其带回实验室进行处理和分析。这两种诊断方式各有优缺点,适用于不同的诊断需求和场景。
5. 常规工况与特殊工况下的诊断
6. 常规诊断与精密诊断
接下来,我们进一步探讨监测与诊断技术的分类。首先,我们可以根据机器的工作状态,将诊断划分为常规工况下的诊断和特殊工况下的诊断。常规工况指的是机器在正常操作条件下的诊断,而特殊工况则可能涉及到机器在异常条件或极限条件下的诊断。
此外,我们还可以根据诊断的深度和精度,将诊断划分为常规诊断和精密诊断。常规诊断通常是初步的诊断,旨在快速识别和定位问题;而精密诊断则更加深入和细致,需要专业的技术和设备来支持。
二、按监测与诊断技术分类
在具体的监测与诊断技术方面,我们有多种选择。例如,振动与噪声监测技术可以通过分析机器运行时的振动和噪声信号来发现潜在问题;超声与声发射监测技术则能够监测裂纹、裂纹扩展以及材料内部缺陷等;红外监测技术利用红外辐射原理及仪器,实时监测机器运行中的温度变化;而润滑油样分析技术则通过分析润滑油样中携带的磨损残留物,来识别机器的故障。这些技术各有其适用范围和优缺点,我们可以根据具体需求选择合适的技术进行监测与诊断。
三、按诊断对象分类
在监测与诊断技术的应用中,我们根据不同的对象进行分类。对于旋转机械,如转子、轴系和汽轮发电机等,我们采用专门的监测与诊断技术来确保其稳定运行。往复机械,包括内燃机、往复式压缩机以及曲柄连杆机构等,也有一套相应的监测与诊断技术。同时,对于工程结构,如框架、桥梁、管道和容器等,我们运用特定的技术来保障其安全性和稳定性。此外,部件如齿轮、轴承和电机等,也有专门的监测与诊断方法来确保其性能和寿命。
四、监测与诊断中的三大关系
定性与定量
定性监测侧重于发现机器异常和初步确定故障位置,其特点是使用简单的仪器,经济实惠,适用于对机器进行一般性的了解。而定量监测则更进一步,通过特定特征来反映机器的异常和故障,并能详细说明故障位置和严重程度,尽管仪器可能更为复杂,但能提供更全面的诊断结论,适合关键和重点机器的监测。
简易与精确
简易诊断主要判断机器是否异常或存在故障,通常使用简单便携的工况监测仪表来区分和判断机器状态。而精确诊断则要求不仅判断机器是否异常,还要深入分析异常的性质、原因和发展趋势,这需要收集更多的诊断信息并借助功能全面的诊断系统。
精确与模糊
随着设备的大型化,其运行状态也变得更为复杂。设备运行状态的变化可能导致各状态之间的界限变得模糊不清。同时,在识别设备的状态及故障时,也存在一定的不确定性。这些因素都要求我们在进行监测与诊断时,既要注重精确性,也要充分考虑模糊性带来的挑战。
1.5 机器零部件失效信息的特点
一、概述
在机器运行过程中,要准确判断其当前状态,明确主导故障及发展趋势,并预测其连续运行时间,我们需要以机器的运行行为为依据。这要求我们首先充分掌握机器零部件运行的各种信息,包括其失效特征、原因及影响等。通过深入分析这些信息,我们才能科学且负责任地回答上述关键问题。
二、机器零部件运行信息的特点
机器零部件的运行信息,是在机器运行过程中产生的各种物理现象的记录。这些信息不仅具有选择性,还伴随着机器的整体运行信息,呈现出既相互联系又相互区别的特点。同时,机器零部件的失效信息往往具有非平稳性,例如发动机连杆磨损产生的间隙,会导致工作中产生非平稳的冲击振动,这种振动与机器的工作方式紧密相关。此外,零部件在失效初期,其运行状态与正常状态非常接近,所产生的失效信息在幅值上非常有限,这种微弱的失效信息往往容易被其他信息淹没,难以察觉。最后,机器系统本质上都是非线性的,但在某些条件下可以简化为线性系统。当机器零部件失效时,其非线性特征会明显表现出来,且随着失效程度的不同,失效信息的表现行为也会大相径庭。
三、机器零部件运行信号的测量
机器零部件的运行信息,是了解其工作状态的关键。在测量机器零部件的失效信息时,我们主要采用两种方法:静态测量法和动态测量法。
静态测量法是直接对机器零部件的失效信息进行测量,其结果直观且可靠,因为所得到的信息直接反映了零部件的失效状况,无需推导计算。但这种方法必须在机器停止且零部件可直接观察,或机器已拆解的状态下进行,因此难以实现工作中的在线测量。
动态测量法则是对表达机器零部件失效信息的动态物理量进行测量。这些动态物理量随时间变化,可能源于零部件的失效,也可能反映机器整体或部分零部件的性能或效能。通过动态测量得到的物理量值或信号,需要经过函数关系运算、变换或加工处理,才能最终获取所需的机器零部件失效信息。
在进行机器零部件失效信号的动态测量时,我们需要关注多个方面,包括选择合适的测量方法、测量参数和传感器,确定最佳的测试点,以及处理信号的放大、消噪等问题。同时,还需要确保测量仪器的正确连接、接地和屏蔽,以确保测量的准确性和可靠性。
四、机器零部件运行信息的提取
有效提取机器的运行信息,是及时发现零部件失效的重要环节。机器零部件的失效信息常通过多种特征量得以体现,这些特征量可能包括产品的功率、油耗等直接功能参数,或是数学模型中的特定系数,如时序模型或状态空间方程的系数,甚至可以通过信息处理方法获得。
特征类型多样,包括简单与复合特征、线性与非线性特征,以及单维与多维特征等。鉴于机器失效信息的多样性、传输选择性、非平稳性和微弱性等特点,在提取特征信息时,需根据不同机器零部件信息的特性,选择适宜的方法。
常用的机器运行失效信息特征提取方法包括信息论方法、平稳与非平稳机器零部件的信息提取、统计模拟方法、主成分分析与核主成分分析、遗传算法与遗传编程、时域平均、盲源分离以及支持向量机等。
五、机器运行信息的有效利用
在获取了机器零部件的运行信息后,如何有效利用这些信息成为了关键。通过深入分析和处理这些信息,我们可以实现对机器运行状态的准确监控,及时发现潜在的故障和问题。此外,这些信息还可以用于优化机器的运行和维护策略,提高机器的使用效率和寿命。
为了更好地利用机器运行信息,需要结合多种技术手段和方法,如数据挖掘、模式识别、人工智能等。这些方法可以帮助我们从大量的数据中提取出有价值的信息,为机器的运行和维护提供科学的决策支持。同时,也需要注重信息的实时性和准确性,确保所利用的信息能够真实反映机器的实际运行状态。
机器零部件故障的识别
机器零部件失效的识别,是信息提取过程中的一项核心任务。零部件的失效常常会导致机器整体功能或性能的改变,这些改变可能直接或间接地反映在机器的运行信息中。通过深入分析和处理这些信息,我们可以准确地确定哪些零部件已经失效,进而有针对性地采取措施,如更换、修复或调整,以恢复机器的正常运行。
2. 机器设计与制造缺陷的识别
机器在设计或制造过程中存在的缺陷,特别是影响机器整体功能的那些,可以通过分析各个零部件或子系统的失效信息来揭示。这种深入的分析不仅有助于发现并指出存在问题的部件,还为设计改进和制造精度的提升提供了宝贵的参考。
工业自动化装备实训台
旋转机械振动分析与控制分析系统
转子系统试验理论与方法验证测试台
轴承、齿轮及传动系统综合故障实训台
转子系统设计制造与运维分析台
轧机关键部件综合故障模拟试验台
大学高水平学科平台
转向架典型故障模拟实验台
转子轴承齿轮典型故障模拟实验台
电机典型故障模拟实验台
机械系内外双转传动子系统实验台
高速列车传动系统的模拟实验系统
机械动力装备平台
可靠性与系统工程学院传动轴系轴承故障实验套件
转子轴承故障试验台
大学新型电力系统源网耦联载荷智能分析系统
机械工业转子装备智能维护技术重点实验
汽车能量回收悬架实验台
理工大学转子试验台
工程大学叶片典型故障模拟测试台
转子系统振动复合环境先进测试平台
旋转机械运行状态模拟实验教学系统
创新创业学院轴承试验台
设备运行状态模拟实验教学系统
风电机组主轴轴承综合实验平台
转子动力学教学实训演示台
多通道数据采集系统
转子故障试验台输入功率提升和控制系统
低速全参数行星齿轮箱故障模拟实验系统
谐波轴承性能检测平台
机械工程控制基础实验台
能源与动力工程学院平台
复杂机电液系统智能运维功能性测试平台
传动系统多功能综合测试平台
轴系激励源识别方法小型验证试验台
轴承高载荷加载及数据采集装置
推进轴系动力学系统采购及服务
全寿命周期齿轮实验台
齿轮全寿命试验台
大型风机缩比控制系统实验台
大型风力发电机组缩比控制系统
转子振动分析与故障模拟试验台系统
机械振动分析与运维试验台
轴系力学测试平台
桌面式齿轮故障教学平台
便携式转子轴承教学实验台
桌面式转子轴承故障教学平台
转子动力学研究实验台
故障机理研究教学平台
转子轴承综合故障模拟实验台诊断台
转子轴承教学平台
机械故障综合模拟实验台
动力传动故障模拟实验台
风力发电传动故障模拟实验台
动力传动故障预测综合实验台
机械故障综合实验台
动力传动故障模拟实验台
风力发电传动故障模拟实验台
电机故障模拟实验台
动力传动故障预测综合实验台
列车转向架故障模拟实验台
轴承预测模拟实验台
本网转载并注明自其它来源(非智慧城市网www.afzhan.com)的作品,目的在于传递更多信息,并不代表本网赞同其观点或和对其真实性负责,不承担此类作品侵权行为的直接责任及连带责任。其他媒体、网站或个人从本网转载时,必须保留本网注明的作品第一来源,并自负版权等法律责任。